A $20.5 million verdict against major welding manufacturers has shaken the industry’s foundations, bringing decades of manganese exposure concerns into sharp focus. The landmark case of welder Jeff Tamraz highlights a growing crisis that threatens both worker safety and corporate stability.
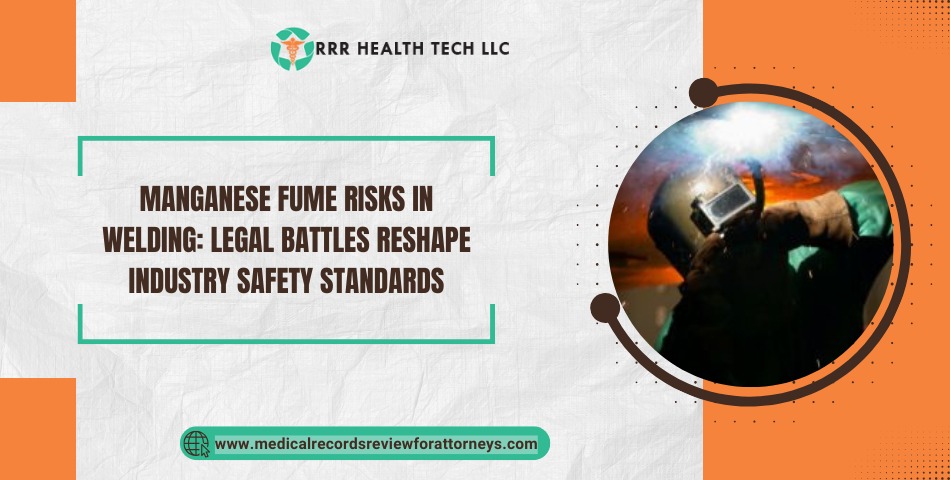
The legal battle over toxic welding fumes represents more than individual compensation claims – it challenges fundamental industry practices and safety standards. As manufacturers face mounting pressure to address manganese toxicity risks, the controversy raises critical questions about corporate responsibility and the true cost of workplace safety.
Legal Challenges and Recent Developments in the Welding Industry
Major welding manufacturers face mounting legal pressure over manganese exposure claims. Lincoln Electric, Hobart Brothers, ESAB Group, TDY Industries, and BOC Group stand at the center of litigation regarding toxic welding fumes. A significant case resulted in a $20.5 million verdict for welder Jeff Tamraz in federal court in Cleveland.
The lawsuit highlighted the companies’ alleged failure to warn workers about manganese toxicity risks in their products. Plaintiffs argue the manufacturers knew about the dangers but did not take adequate steps to protect welders. The companies maintain there is insufficient evidence linking welding fumes to neurological disorders and have appealed the verdict.
These legal actions raise questions about manufacturer liability and workplace safety standards. The outcomes could affect how welding companies label their products and implement safety protocols. Industry observers note these cases may lead to stricter regulations for manganese exposure limits.
The lawsuits seek both compensation for affected workers and changes in manufacturing practices. Some legal actions aim to stop the production and sale of welding products containing dangerous levels of manganese. The financial implications for welding companies could be substantial, potentially affecting product development and safety measures across the industry.
Health Risks Associated with Manganese Fume Risks in Welding
Manganese exposure from welding fumes poses serious health concerns for workers across multiple body systems. The toxic metal affects the lungs, liver, kidneys, and central nervous system. Male reproductive health also faces risks from prolonged exposure.
Workers exposed to manganese often report mood changes and memory problems. Even at levels below 0.2 mg/m3, welders may experience decreased hand-eye coordination and slower reaction times. These symptoms can appear gradually, making early detection challenging.
Long-term exposure to manganese fumes can lead to symptoms similar to Parkinson’s disease. This condition affects movement control and can cause tremors in exposed workers. The medical community recognized these risks as early as 1932, when Dr. Erich Beintker published findings on manganese effects from arc welding.
The symptoms’ severity often correlates with exposure duration and concentration levels. Medical experts stress that even low-level exposure over time may cause lasting neurological damage. This presents particular concerns for career welders who face daily exposure risks.
Current safety guidelines may not fully protect workers, as research indicates harmful effects at concentrations below existing limits. These findings highlight the need for strict monitoring and protective measures in welding environments.
Historical Context of Manganese Toxicity
The scientific community’s understanding of manganese toxicity in welding dates back to 1932, when Dr. Erich Beintker documented the effects of arc welding fumes. His research marked the first systematic examination of manganese-related health issues in the welding profession.
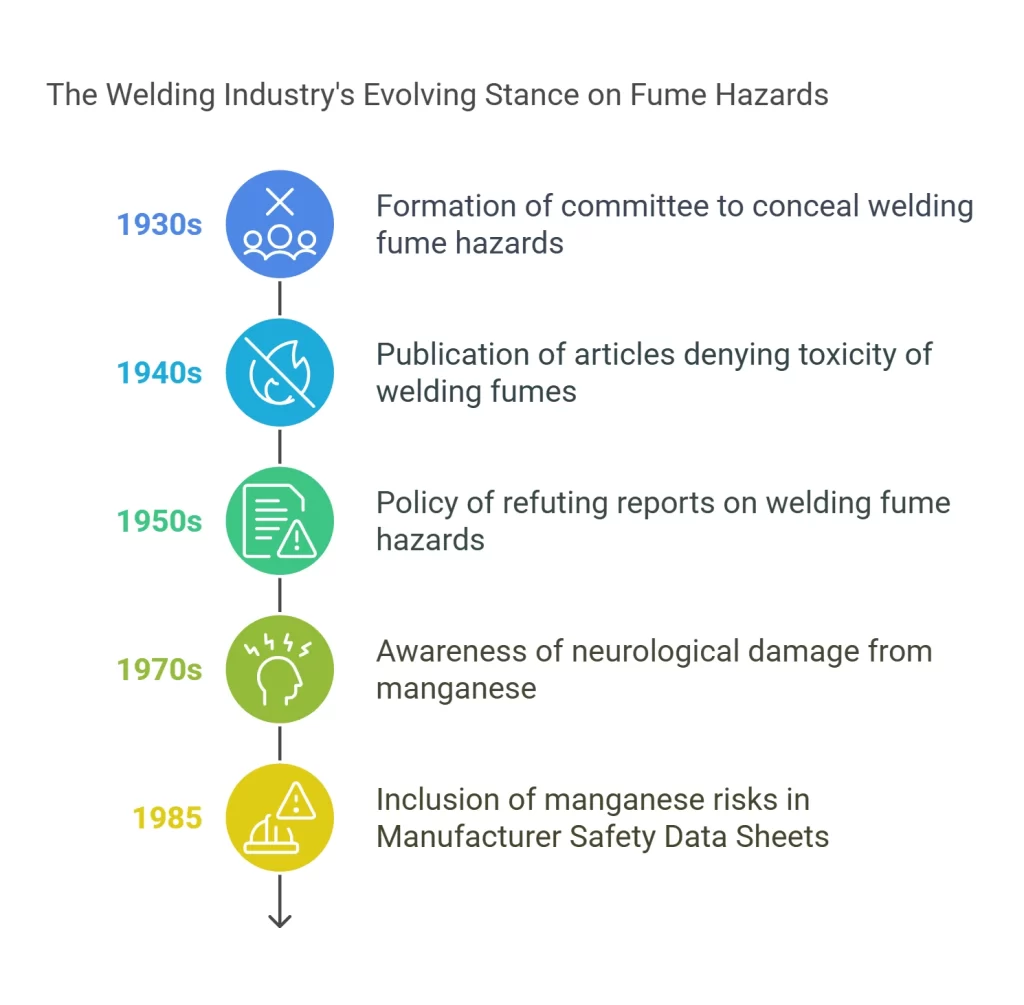
The Metropolitan Life Insurance Company built upon Beintker’s work in 1937, publishing a detailed booklet about manganese poisoning risks. This publication brought attention to the occupational hazards welders faced, leading to increased scrutiny of workplace conditions.
By 1943, industry publications like Occupational Hazards Magazine began addressing manganese exposure directly. The magazine published articles warning about manganese dangers, showing growing awareness within the industrial sector. These early warnings contradicted later claims by welding companies that manganese risks were unknown.
Despite this historical evidence, welding manufacturers maintained their position that manganese amounts in fumes posed minimal health threats. Company representatives stated the industry “acted responsibly” regarding safety concerns. However, documentation from the 1930s and 1940s suggests manufacturers had access to information about manganese-related health problems.
Early research findings continue to influence modern legal cases and safety regulations. The historical record shows a pattern of documented concerns about manganese exposure, dating back nearly a century.
Industry Response and Accusations
Welding manufacturers maintain that manganese levels in their products remain too low to cause harm. When faced with health-related lawsuits, major companies like Lincoln Electric and ESAB Group stated the industry has followed proper safety protocols throughout its history.
Company representatives argue the scientific evidence doesn’t support claims linking welding fumes to neurological disorders. They point to studies questioning the connection between standard welding practices and manganese-related illness. The manufacturers say their warning labels and safety documentation meet all regulatory requirements.
However, legal documents show allegations that companies withheld information about manganese fume dangers. Plaintiffs’ attorneys present evidence suggesting manufacturers knew about health risks but didn’t properly inform workers. These accusations center on internal company documents and industry communications spanning several decades.
The debate extends to trade organizations’ roles in addressing safety concerns. Critics say these groups minimized potential health impacts while promoting industry interests. Current investigations examine whether manufacturers and industry groups properly communicated known risks to workers and regulators.
The controversy has sparked renewed attention to workplace safety standards and manufacturer liability. As legal proceedings continue, the industry faces pressure to address historical handling of manganese exposure concerns.
Legal Recourse and Importance of Statute of Limitations
Welders who experience symptoms related to manganese exposure should seek medical evaluation promptly. Signs of neurological problems, memory issues, or movement difficulties warrant immediate medical attention. Quick action helps establish documentation for potential legal claims.
The class action lawsuit against welding product manufacturers aims to address manganese poisoning concerns. Legal proceedings focus on stopping the manufacture and distribution of welding products with dangerous manganese levels. Attorneys stress that affected workers must file claims within specific time frames set by state laws.
Medical records play a central role in these cases. Doctors’ documentation of symptoms, work history, and exposure levels strengthens legal claims. Workers should maintain detailed records of their welding activities, protective equipment use, and workplace conditions.
Time limits for filing claims vary by jurisdiction. Missing these deadlines can prevent workers from seeking compensation, regardless of injury severity. Legal experts recommend consulting attorneys experienced in occupational exposure cases to understand filing requirements.
The legal process typically includes medical examinations, workplace assessments, and review of safety protocols. Courts examine both current and historical evidence of manganese exposure. These cases often require testimony from medical experts who can link symptoms to workplace exposure.
Economic and Safety Implications for the Welding Industry
The legal challenges over manganese fumes create substantial financial risks for welding manufacturers. Multi-million dollar verdicts and ongoing litigation costs affect company operations and product development. Industry analysts predict these expenses could lead to higher product prices and increased insurance premiums across the sector.
Safety regulations face potential changes as lawsuits highlight worker protection gaps. Manufacturers may need to implement stricter testing protocols and expand warning labels. The costs of enhanced ventilation systems and respiratory equipment could impact both manufacturers and end-users.
Companies now evaluate their control measures for fume exposure. Required changes include improved local exhaust ventilation, better air monitoring systems, and enhanced personal protective equipment. These modifications represent significant investments for businesses throughout the supply chain.
The focus on manganese exposure has prompted regulatory agencies to review current workplace standards. Some experts suggest lowering permitted exposure levels, which would require additional safety investments. Small welding operations face particular challenges meeting stricter requirements while maintaining competitive pricing.
These developments signal a shift toward greater accountability in the welding industry. Companies must balance worker safety concerns with operational costs, leading to new approaches in product design and workplace protection measures.
The Path Forward: Balancing Safety and Industry Progress
The welding industry stands at a critical crossroads as it grapples with manganese fume risks and their far-reaching implications. The outcome of current legal battles will likely reshape safety protocols, product development, and regulatory standards for years to come. Manufacturing practices that once went unquestioned now face intense scrutiny.
The challenge lies in finding solutions that protect workers without crippling an essential industry. As companies invest in enhanced safety measures and improved product designs, the transformation may ultimately lead to a safer, more sustainable welding sector. The industry’s response to these challenges will define its future and set new standards for workplace safety.